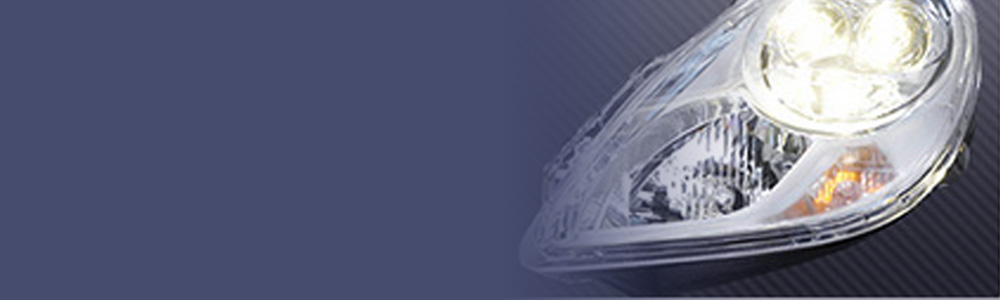
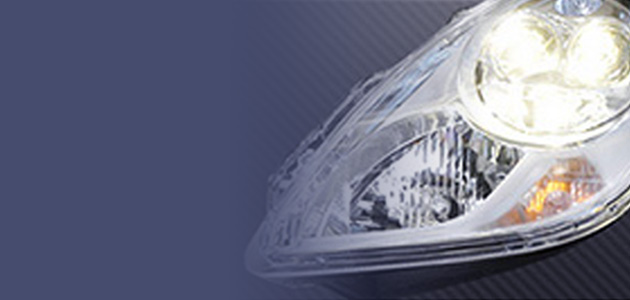
世界初の量産型電気自動車に搭載!
スタンレー初となるLEDヘッドランプの量産が、2009年6月にスタートした。完成品は世界初の量産型電気自動車に搭載される。
2000年にLEDヘッドランプの開発を始めてから約10年、失敗と成功を繰り返し、遂に成し遂げた悲願だ。特に受注してからの1年あまりは、未知のトラブルが続く中、時間との戦いを制してきた。
プロジェクト成功の背景には、スタンレーの伝統的な社風と、社員たちのあふれる情熱があった。
2000年代に入りLEDの性能は一気に向上し、さまざまな製品で利用されるようになった。2008年には自動車用のLEDヘッドランプが、ほぼ実用化できる状態にまで仕上がっていた。「省電力・長寿命のLEDヘッドランプを、一日も早く市場に出したい」との思いで、自動車メーカー各社に提案を続けてきたスタンレー。甲斐あって、世界初の量産型電気自動車に採用されることが決まった。世界中から注目されるエコカーのコンセプトに、LEDはピタリとマッチする素材だったのだ。
とはいえ、納品までに時間の猶予はない。LEDの生産、LED回路の開発、LEDユニット部分の生産準備、ヘッドランプ組み立ての生産準備を、複数の事業所でほぼ同時進行で進めた。
このように目標に対する強い意志で全社が一丸とならなければ、タイトなスケジュールを乗り切ることはできなかっただろう。
「未経験の製品を短納期で」という難しいプロジェクトを成功させるためには、社員たちのアイデアあふれる提案が欠かせなかった。特に生産を効率化したスタンレー初の試みを、3つ紹介しよう。
1.工程要件図
LEDヘッドランプの生産では初めて使う設備や部品が多く、しかも繊細な扱いが求められる。そこで、現場での困難をあらかじめ予測し、部品の入荷から組立、検査、出荷までをまとめた「工程要件図」を作成。生産ラインの効率アップに努めた。
2.ゴミの付着を防ぐ特製容器
LEDモジュールにとって、一番の問題はゴミの付着。特に輸送時はゴミが付着しやすい。そこで考案されたのがモジュールを保護する特製の袋だ。それに加えて輸送用の箱にも静電気の発生を防ぐ特殊な素材を採用し、万全のゴミ対策をしている。
3.簡易配光検査装置
組立現場用に、製品が配光の規格を満たしているか(必要な範囲を照らしているか)を検査する装置を新たに開発。工程内で検査ができるので、生産効率は格段に向上している。
LEDヘッドランプの量産が実現するまでには、想定外のトラブルが多く発生した。たとえば、ランプを点灯すると端の方で色が分離し、青い光が出てしまう「色分離」の問題だ。凸レンズの形状を検証・分析することにより最適な条件を導き解決した。
自動車のランプは国ごとに異なる法規の要件をクリアし、認可(免許)が下りなければ販売はできない。特に厳しいヨーロッパの基準に適合させるため、細心の注意を払って開発が進められた。
しかし開発スケジュールが短いため、認可の取得準備に時間的な余裕はなかった。
スタンレーはランプの開発と平行して、認可当局と当社初のLEDヘッドランプの試験方法の調整と交渉に奔走し、全ての力がひとつになった結果、最短時間でヨーロッパの認可を取得。その後、日本国内での発売に向けた審査にも合格し、遂にLEDヘッドランプの実用化を成し遂げた。
得意先の担当者には、デザインの検討や試験を共同で実施するために、何度もスタンレーへ足を運んでいただいた。両社の密な連携があったからこそ、短納期での量産が実現したのだ。得意先からは量産開始を前にして、「この短納期でよくぞここまでやってくれた。スタンレーの底力を見た」との言葉をいただいている。スタンレーのスタッフを大いに励ます一言だ。
今後はさらなる光量のアップとともに、材料や部品点数の見直しによりコストダウンを図っていく。高価格がネックといわれる電気自動車を普及させる助けになるはずだ。
より優れたヘッドランプを開発するため、スタンレーの挑戦は今日も続いている。